X-55 Advanced Composite Cargo Aircraft
In the mid-1990’s, the Air Force Research Laboratory (AFRL) acknowledged that even though there was tremendous potential for the incorporation of advanced composites to reduce aircraft structural weights compared to conventional metal structures, the industry was hesitant to implement them in new aircraft.
As a result of this hesitation, AFRL launched the Composites Affordability Initiative (CAI) to address the perceived risks and barriers. Government labs including NASA worked collaboratively with industry to develop advanced materials and manufacturing technologies. This 10-year AFRL-led research and development effort ultimately led to the Advanced Composite Cargo Aircraft (ACCA) experiment.
The ACCA was conceived by AFRL as a fast-track, low-cost development effort. ACCA was designed in 5 months, then built and flown 20 months after the go-ahead at half the estimated cost of a conventional design of the same size.
Interestingly, the ACCA started out as a Dornier 328 regional airliner whose fuselage and vertical tail were removed and replaced with a new all composite design structure specifically tailored for the air mobility mission.
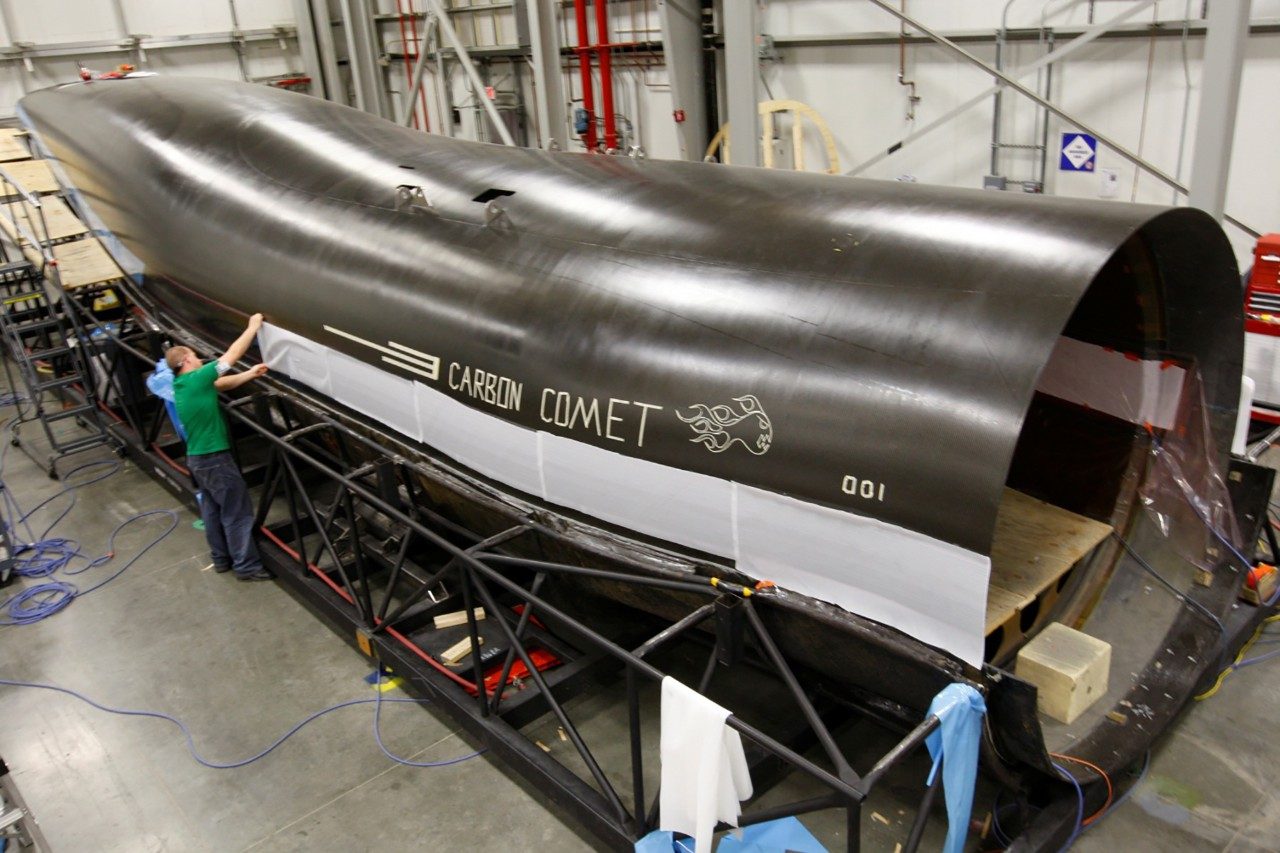
Yes, the Skunk Works approach to the ACCA program involved cutting apart a perfectly good aircraft.
AFRL had just $50 million set aside for this advanced composite manufacturing program and many in industry felt that it would be impossible to develop a composite cargo aircraft for that amount. The team at Skunk Works decided it was possible but only if they used an existing aircraft to cut costs.
In the spirit of exploration and in an effort to demonstrate and test the technologies while keeping costs down and on schedule, the small team modified the high-wing Dornier jet, mating its existing engines, wing, landing gear and avionics systems to the new composite structure.
The program demonstrated the feasibility of designing and manufacturing large, bonded unitized structures featuring low-temperature, out-of-autoclave curing. The fuselage was constructed in two large half-sections (upper-lower) featuring sandwich construction with MTM-45 skins and Nomex core, bonded together with adhesive and ply overlays along the longitudinal seam rather than numerous frames, stiffeners and metal fasteners used commonly in traditional aircraft. The vertical tail was designed using tailored stiffness technology. These were joined with the existing Dornier 328J cockpit, wing, engines and horizontal tail.
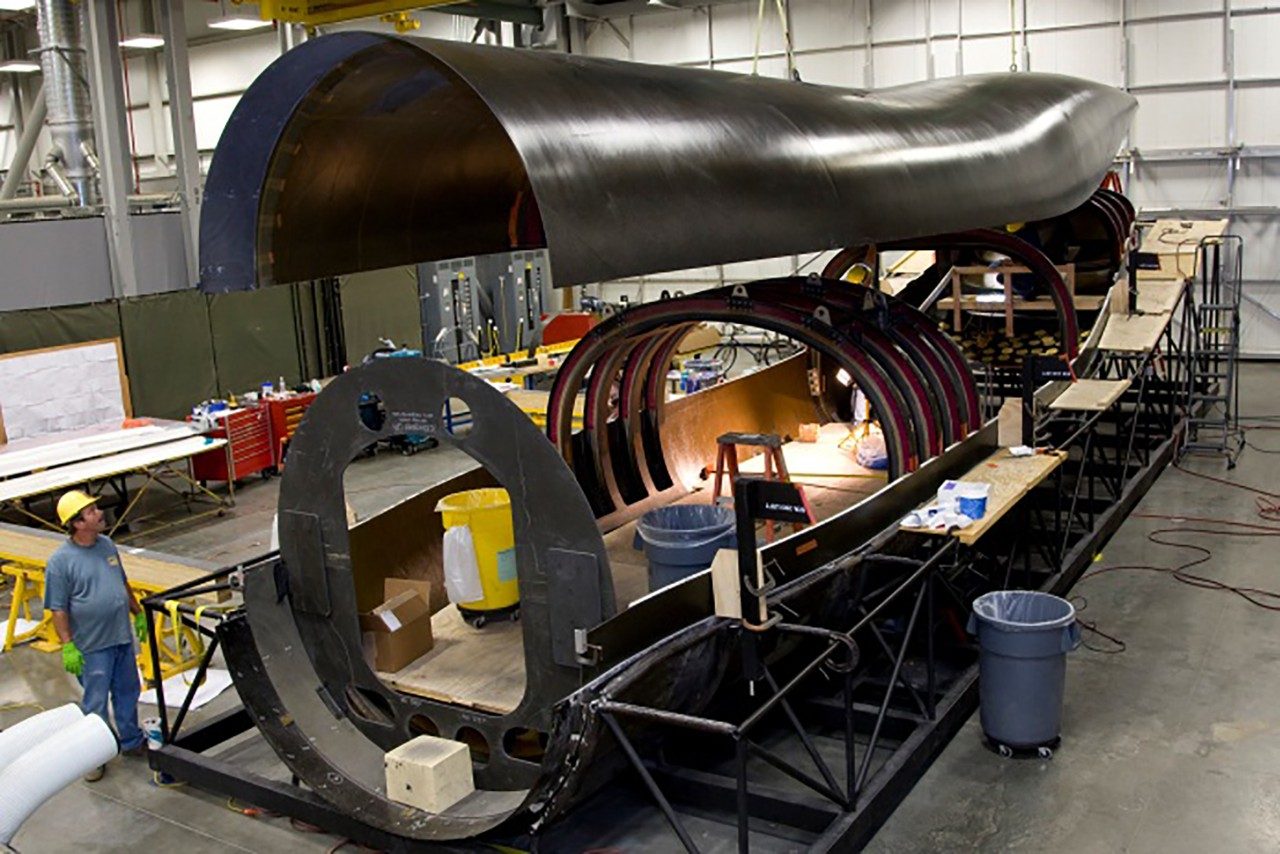
Compared to the original metallic components, the composite structure used approximately 300 structural parts versus 3,000 metallic parts and approximately 4,000 mechanical fasteners compared to 40,000.
The ACCA design is representative of a military transport type aircraft able to carry standard military cargo pallets, passengers or small vehicles.
It is the first of several steps intended to advance the readiness of multiple technologies needed for the next generation of theater airlift aircraft. The ACCA demonstrates how future aircraft designs and manufacturing processes can be tailored through the use of advanced composites and new structural concepts to significantly shorten design spans, reduce aircraft size and structural weight, accelerate manufacturing processes, reduce tooling costs and reduce assembly labor. Initial estimates suggest development cost could be reduced by 25 percent or more over today’s processes plus additional operating cost savings from less weight resulting in lower fuel burn.
Historically, aircraft cost has been determined by the size and weight of the vehicle. With ACCA we are proving that while size does matter, it isn't the be-all, end-all determination of aircraft cost.